Pelletisation Equipment
Brochure
Download our document to see specific data of the product and how we work.
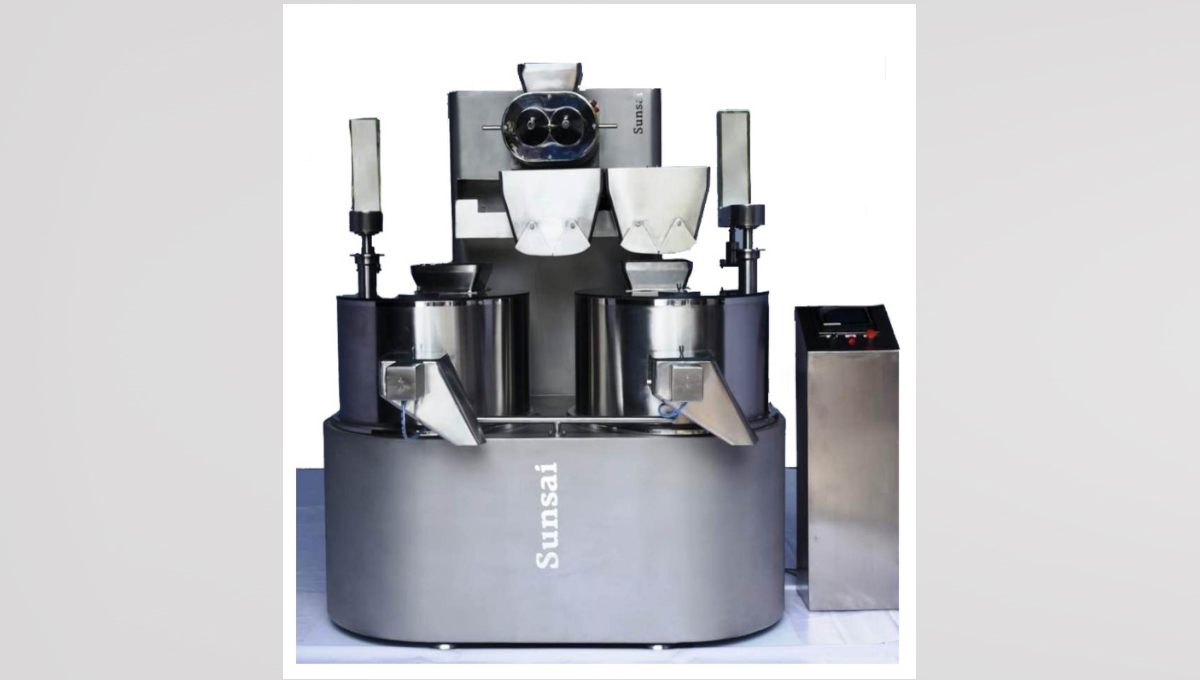
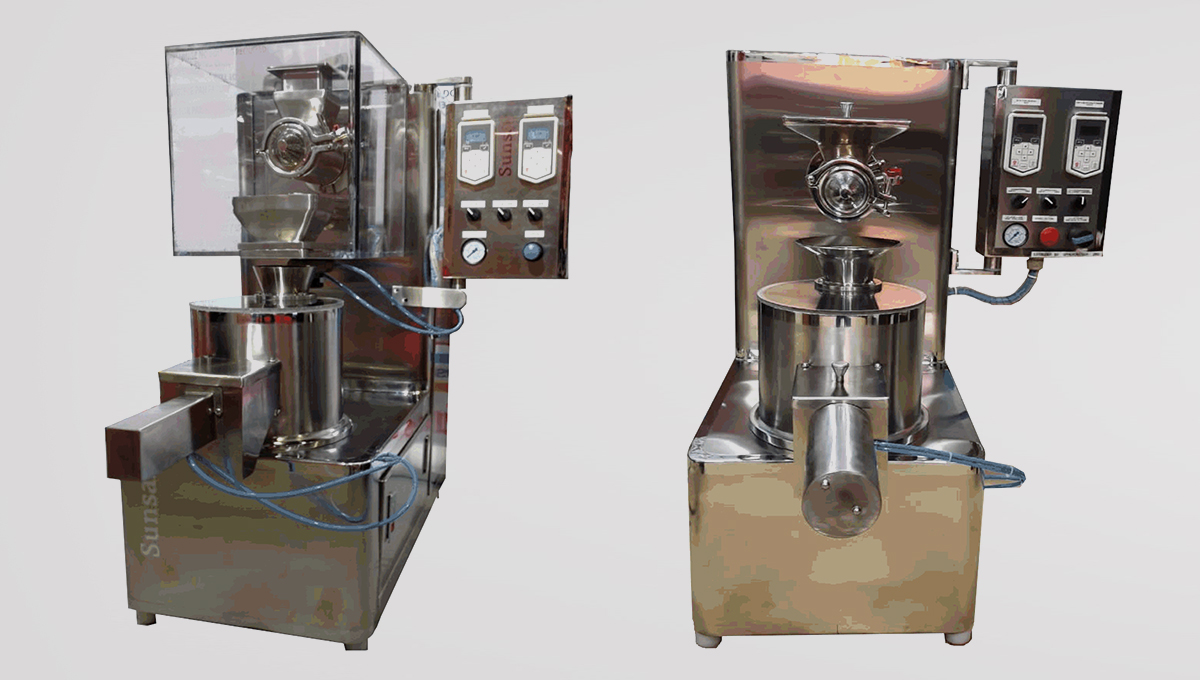
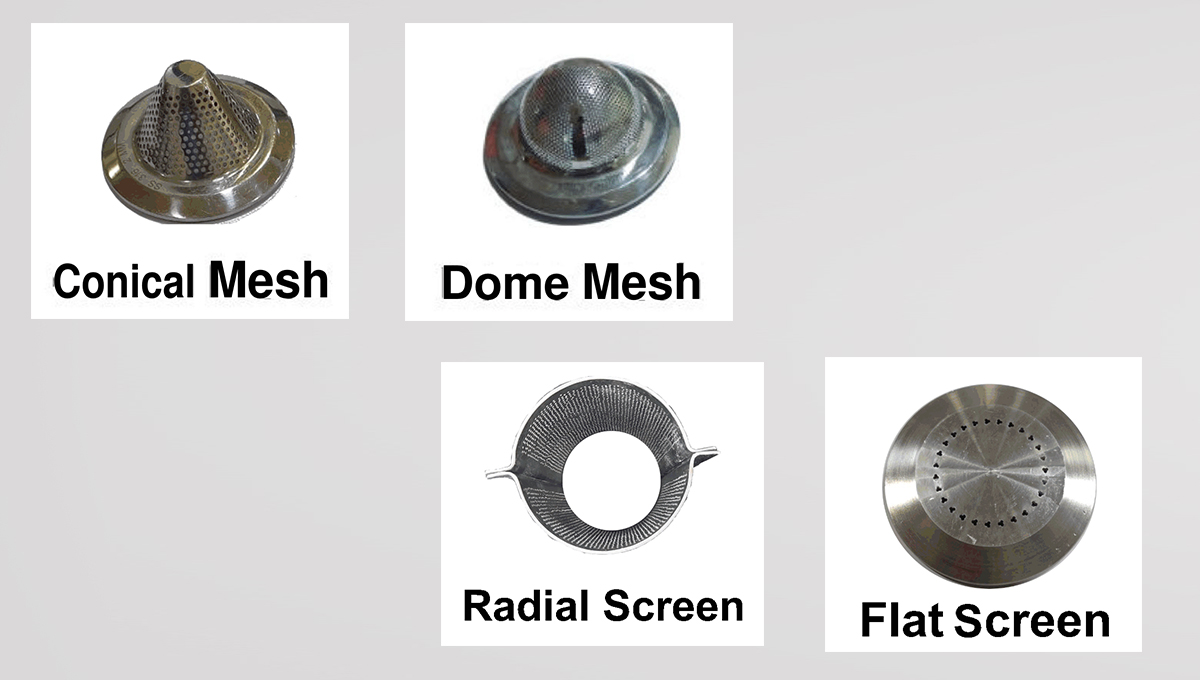
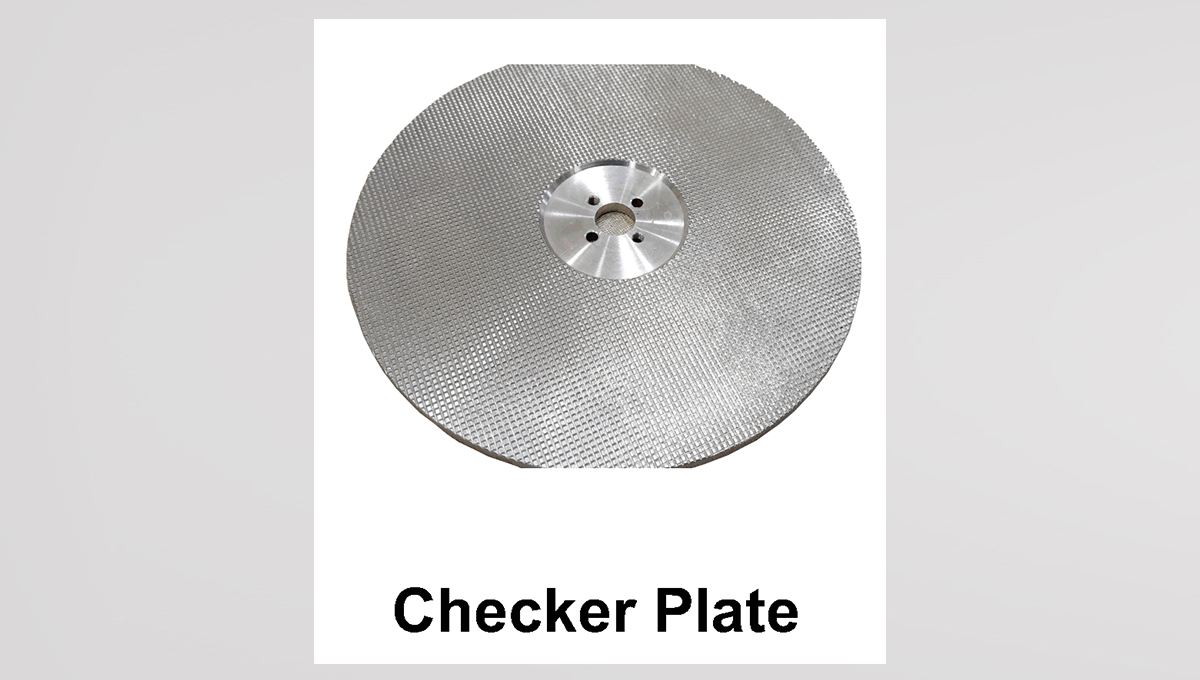
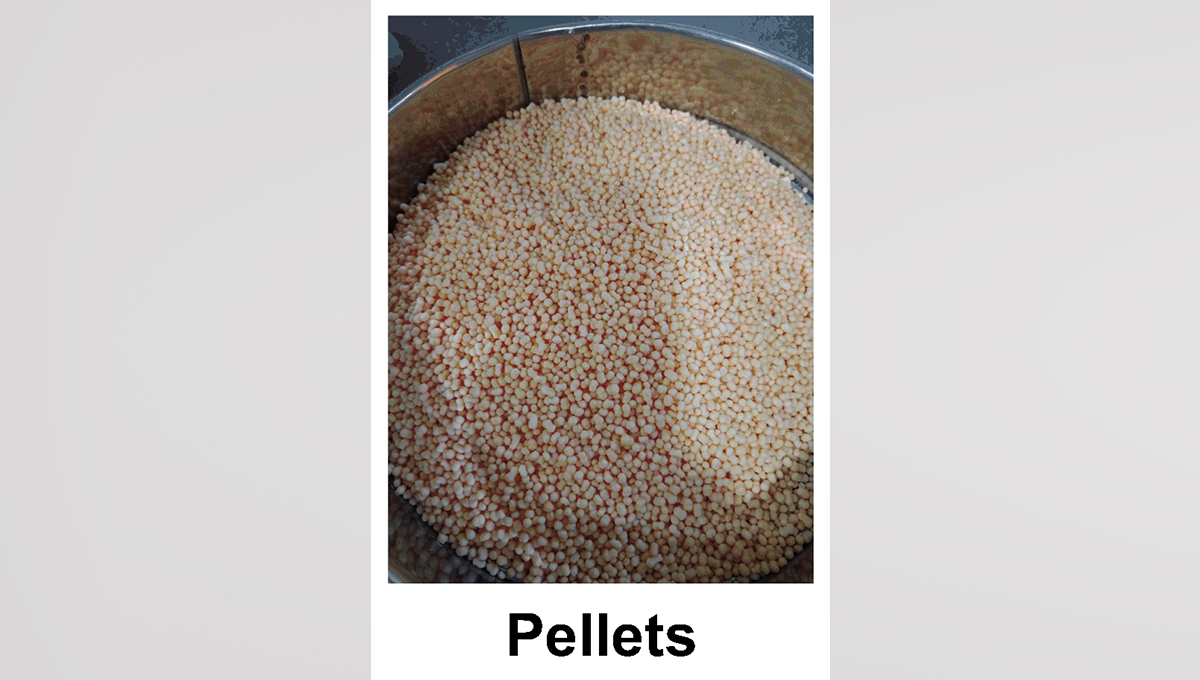
Extruder - Spheroniser
The Extruder-Spheronisation process is commonly used in the pharmaceutical industry to make uniformly sized spheroids. It is especially useful for making dense granules for sustained controlled- release solid dosage oral forms with a minimum amount of excipients.
Extruder is a first step in the extruder-spheronisation process. The size of the extruder screen aperture will dictate the approximate size of the resulting spheroids. However, extruder is often used to eliminate dust in formulations even when spheronisation is not the final objective.
Spheronisation has many advantages & the process is useful in several ways: it can improve the product; simplify manufacturing processes and help to reduce costs.
The process is well known and widely used in the pharmaceutical industry but spheronisation is becoming increasingly recognized in other areas of industrial materials handling.
The size of the spheres are determined by the diameter of the extrudes used for the spheronisation process.
The most common groove pattern used for spheroniser discs is the square cross-hatched square design, where the processing surface is covered with a grid of truncated pyramids.
Extruder
Model | Working Capacity |
---|---|
EXT-20 | 50-100 Grm. |
EXT-30 | 100-500 Grm. |
EXT-60 | 2-3Kgs. |
TSEXT-100 | 30-50Kgs |
TSEXT-130 | 75-100Kgs. |
Spheroniser
Model | Working Capacity |
---|---|
SPH-75 | 25-50Grm. |
SPH-150 | 50-100Grm. |
SPH-250 | 1-2Kgs. |
SPH-500 | 15-25Kgs |
SPH-700 | 40-50Kgs. |
Fully Automatic Integrated System |
TSEXT-100: 1 No. with SPH-500: 2 Nos. |
TSEXT-130: 1 No. with SPH-700: 2 Nos. |